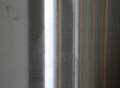
The most popular finish in stainless steel fabrication is the No 4 finish--the easiest to maintain and one with a nice surface appearance. A No 4 surface is produced by cutting the surface with coated abrasive belts to remove a very small amount of metal without affecting its thickness. Because it is directional, it allows for easy matching of surfaces. The "official" definition of a No 4 finish is "a linearly textured finish that is produced with mechanical polishing. The average surface roughness (Ra) may generally be up to 25 micro-inches (0.64 micrometeres)."
The Specialty Steel Industry of North America has set guidelines for polished finishes on stainless:
No 3: An intermediate polished surface obtained by finishing with a 100 grit abrasive. Generally used where a semi finished polished surface is required. A No 3 usually receives additional polishing during fabrication.
No 4: A polished surface obtained by finishing with a 120-150 grit abrasive, following initial grinding with coarser abrasives. This is a general purpose bright finish with a visible "grain" which prevents mirror reflection.
With the introduction in recent years of non-woven abrasives, many fabricators are also using a medium non-woven belt to achieve the No 4 finish. If you have other questions regarding finishing stainless, please feel free to call Abrasive Resource at 800-814-7358, or visit us online at: www.abrasiveresource.com